Always the perfect fit, without any waste
You're looking for aluminum plates that are ready to use — with no waste or post-processing. With our Custom-Cut Aluminium Sheets, you receive precisely cut plates tailored to your application. It saves time, reduces costs, and boosts efficiency.
At MCB, we specialize in precision cutting of cast and rolled aluminum plates for the machining industry.
To further support the growing demand for Custom-Cut Aluminium Sheets, we've installed a new, state-of-the-art saw: the FM12.
Our new saw, your new possibilities
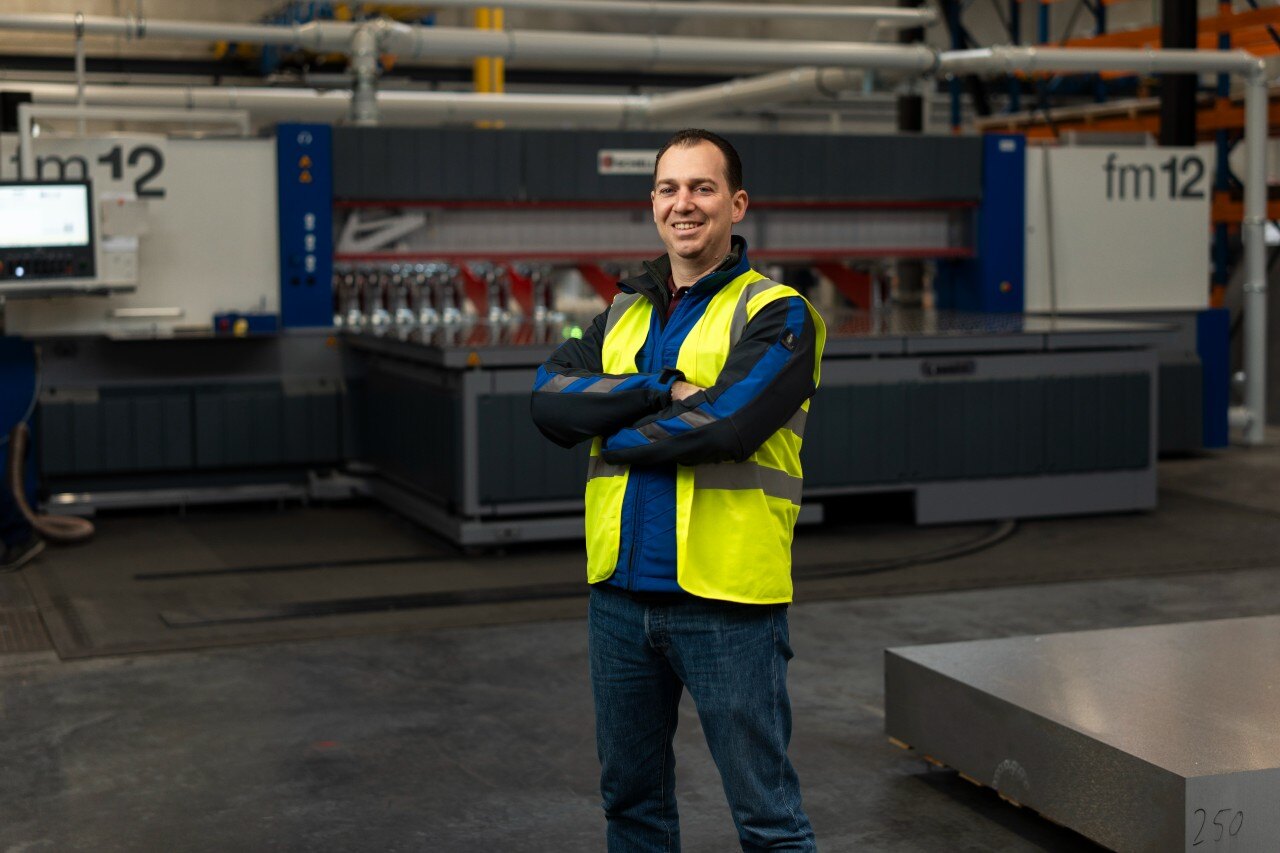
With the installation of our new saw, we can now cut aluminium plates up to 4020 x 2020 mm in size and up to 250 mm in thickness. Thanks to this expansion, we can guarantee delivery times of 48 hours within Belgium and 72 hours within the Netherlands.
Strict quality control
After cutting, each plate undergoes a thorough inspection to ensure a dimensional tolerance of approximately 0.5 mm in both length and width, as well as guaranteed squareness of the material.
What can you expect from us?
We understand how crucial precise sawing tolerances are for machining — and the benefits they bring you:
- Efficiency in Machining
The more precisely your base material is cut to size, the less post-processing is required. This reduces time waste and tool wear. - Less Material Waste
Incorrectly sized plates — whether too large or too small — can lead to additional processing steps or unusable parts, resulting in material loss. - Consistent Quality of Final Products
Tight tolerances ensure that the end products meet specifications — critical in sectors such as aerospace, automotive, and high-tech industries.
- Improved Clamping and Stability
Accurately cut plates fit better in clamping devices, reducing vibrations and inaccuracies during machining. - Automation and CNC Machining
Modern CNC machines use highly accurate CAD/CAM programs and are increasingly automated. This requires materials to be delivered not only in the correct dimensions, but also square, clean, and burr-free. If initial measurements are off, it can cause deviations and machine downtime. - Cost Savings
Less rework, reduced tool wear, and lower material waste contribute to lower overall production costs.
Our Standard Alloy Selection
EN AW-6082-T6/T651 (Rolled)
EN AW-6082 – AlMgSi1 is an aluminium alloy from the 6000 series, commonly used in machine construction and for machine parts. The alloy is highly machinable, making it ideal for precision operations such as milling. Additionally, it has good technical anodizing properties, although a uniform decorative finish cannot be guaranteed.
While EN AW-6082 offers reasonable corrosion resistance, it is less resistant compared to some other aluminum alloys, such as EN AW-5083. The alloy is easy to machine but difficult to deform, making it less suitable for applications requiring bending or deep drawing. Despite these limitations, it remains a popular choice for structural applications where strength and machinability are important.
EN AW-7075-T651 (Rolled)
EN AW-7075 – AlZnMgCu1.5 is an aluminium alloy known for its exceptional mechanical properties and strength. It belongs to the 7000 series and contains zinc and copper as its primary alloying elements, resulting in very high tensile strength and hardness. This makes it widely used in aerospace, heavily loaded machine parts, and defense and weaponry applications.
The alloy is highly machinable but difficult to form, making it less suitable for applications requiring bending or deep drawing. Due to its high copper content, EN AW-7075 has lower corrosion resistance, and technical anodizing is recommended, although a decorative finish cannot be guaranteed. Nevertheless, this alloy remains a top choice for applications demanding maximum strength and wear resistance.
EN AW-5083
(Cast & 6-sided saw-cut)
EN AW-5083 – AlMg4.5Mn is a cast and 6-sided saw-cut aluminium alloy distinguished by its excellent machinability and good corrosion resistance. Thanks to its high magnesium content, this alloy is particularly suitable for applications in mold and machine construction where strength and durability are required.
This low-stress alloy is technically anodizable and offers reasonable formability, providing flexibility in various machining processes. The thickness tolerance of -0/+3 mm is relatively wide, as this grade is often further processed to achieve the desired final thickness. This makes EN AW-5083 especially suitable for precision applications where accurate dimensions and post-processing are crucial.
EN AW-5083
(Cast & milled + PVC)
EN AW-5083 – AlMg4.5Mn is a low-stress, cast and milled aluminium alloy with excellent machinability and high corrosion resistance, making it ideal for applications in mold and machine construction. Thanks to its high magnesium content, it is well resistant to environmental influences and suitable for technical anodizing.
The material offers reasonable formability, allowing for flexible use in various machining processes. An important advantage is the precise thickness tolerance of ±0.1 mm, regardless of the plate thickness, ensuring high dimensional accuracy and reduced need for post-processing. The addition of a PVC protective film on both sides helps to protect the surface during transport and handling.
EN AW-5083-H111 (Rolled)
EN AW-5083 H111 is an aluminium alloy known for its excellent corrosion resistance, making it ideal for applications in demanding environments. The material offers good machinability and is suitable for technical anodizing, providing extra protection and improved surface finish.
Additionally, this alloy has reasonable formability, allowing for easy processing without significantly compromising its structural properties. Due to these characteristics, EN AW-5083 H111 is widely used in shipbuilding, transportation equipment, and storage tanks, where durability and resistance to environmental influences are crucial.
EN AW-2017-T451 (Rolled)
EN AW 2017 T451 is a copper-containing aluminium alloy. Due to its high copper content, this alloy offers higher strength compared to many other aluminum types. Additionally, the material has good machinability, making it suitable for applications requiring precise machining.
A key consideration is its lower corrosion resistance because of the copper content, often necessitating additional surface treatments such as (technical) anodizing. Furthermore, the weldability of EN AW 2017 is moderate, making it less suitable for welded constructions.
Because of the combination of strength and machinability, this alloy is widely used in machine building and aerospace industries, where precision and structural strength are critical.
EN AW-ALPLAN 6082
(Rolled & machined + PVC)
EN AW-ALPLAN 6082 – AlMgSi1 is a rolled and machined aluminium alloy distinguished by its excellent dimensional stability and high precision. Thanks to its uniform microstructure and tight rolling patterns in both the longitudinal and transverse directions, this material offers an exceptionally flat surface without irregularities.
A key advantage of ALPLAN 6082 is its outstanding suitability for decorative anodizing in all colors, making it ideal for applications with high aesthetic demands. Moreover, it has a precise thickness tolerance of +/- 0.1 mm, regardless of plate thickness. Because of these properties, this alloy is widely used in high-end products where both precision and a flawless anodized finish are essential.
Alloys on request
Our Machinery
Our machine park consists of 3 Schelling aluminium panel saws:
- Schelling FTM: cutting capacity up to 150 mm thickness with a maximum length of 3020 x width 1520 mm
- Schelling FM10: cutting capacity up to 200 mm thickness with a maximum length of 3020 x width 1520 mm
- Schelling FM12: cutting capacity up to 250 mm thickness with a maximum length of 4020 x width 2020 mm
With our machines, we are able to saw panels with a minimum length and width of 20 mm. From a thickness of 5 mm, we saw plates supplied without minimum order quantity.
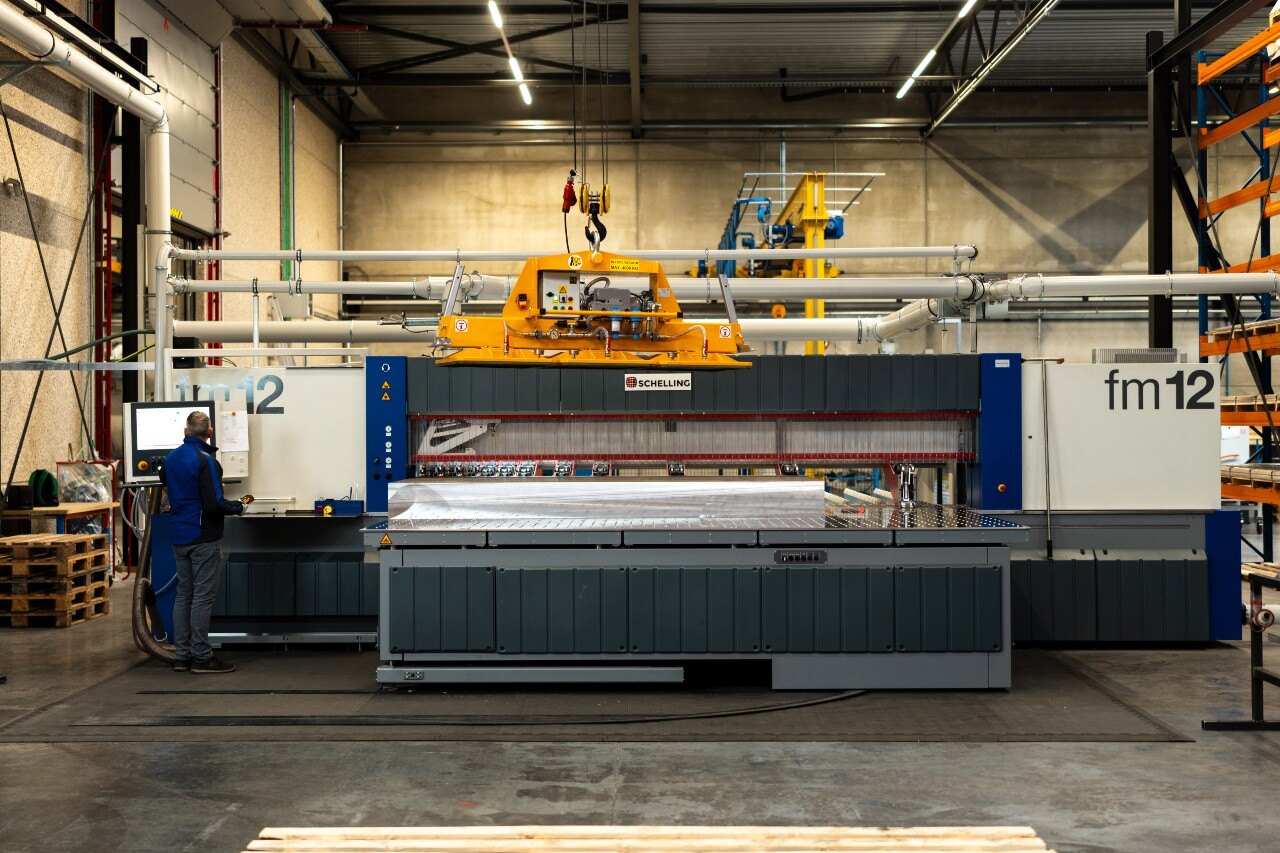
Sustainability in Focus
We have invested in a briquette press to process our leftover materials more efficiently. When cutting large aluminum blocks, chips and scrap material are generated. The chips are collected and compressed into briquettes, making them more compact and easier to transport to our scrap dealer. The remaining scrap material is partly sent to the scrap dealer and partly supplied to a supplier who melts it down into new base material. This circular approach aligns with our sustainability vision.
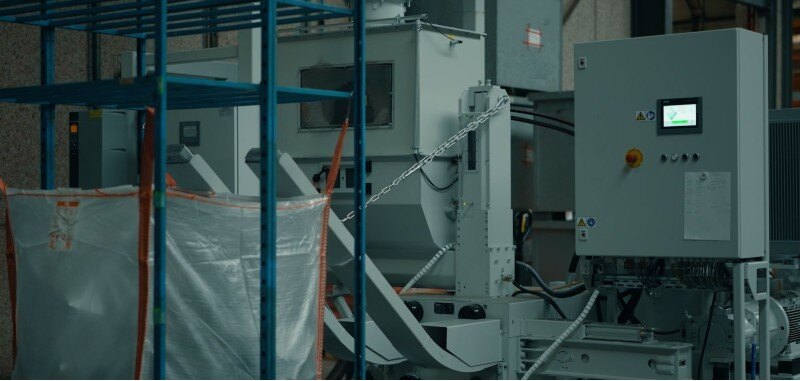